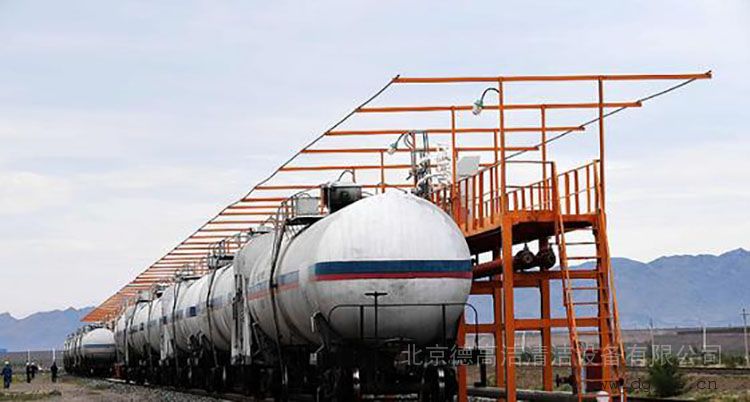
铁路槽车蒸汽进行的特洗,在我国应用比较广泛,但其工艺流程多年来几乎没有多大变化。高压水铁路槽车特洗工艺目前正在逐步开始推广应用,相比旧的蒸汽特洗工艺,我们进行比较后得出了以下结论。
1、高压水清洗效率高,效果好
用蒸汽特洗工艺对槽车进行清洗,洗一台车一般约需10h,而用高压水特洗工艺只需40~70 min,工作效率平均提高了近十倍,并且洗车效果明显优于蒸汽特洗。
2、高压水清洗能耗低,成本低
用
高压水射流清洗罐车,比如装C8、C9、裂解汽油、苯、芳烃等的罐车,每台车仅耗水4~7t,耗电72~125 kw·h。而蒸汽特洗罐车可分2种情况,一种是人工特洗原装柴油、润滑油的罐车,用气量相对少些,一般每台车不超过1t蒸汽,新鲜水约用1t左右;另一种是装化工原料的罐车,清洗这种罐车时每台车要用8h,消耗蒸汽约5t。这样高压水特洗工艺相比蒸汽特洗工艺每台车要节约400元左右的洗车成本。
3、高压水特洗工艺投资少
我们以2个台位的高压水铁路槽车特洗设施为例,它的年洗车能力可以达到3000台,而要达到相同的洗车能力,蒸洗台位至少需要8个;而它们的投资约是1 : 2。
4、高压水特洗工艺解决了大气污染问题
采用蒸汽蒸洗的槽车特洗工艺,由于罐车并不密封,罐车内的残存物质在高温的作用下,使其带挥发性的物质扩散到大气中,尤其是一些沸点较低、挥发性较强的有机化合物,受热后从罐口处迅速挥发排放到大气中,直接严重污染大气,使工作环境严重恶化,操作工人身受其害;而高压水特洗技术采用了密封清洗工艺,将罐内残余物质冲洗下来随液体排放到污水处理场进行处理。由于温度不高,其挥发出来的物质也大大减少,而且废气抽出净化合格后才排人大气中,从而解决了大气污染问题,很大程度改善了洗罐站工人的工作条件。
由此可见,无论从理论上分析还是实际的运行过程都证明,高压水铁路槽车特洗工艺效率高、投资少、节约能源,而且对环境无污染,非常适合大面积推广。